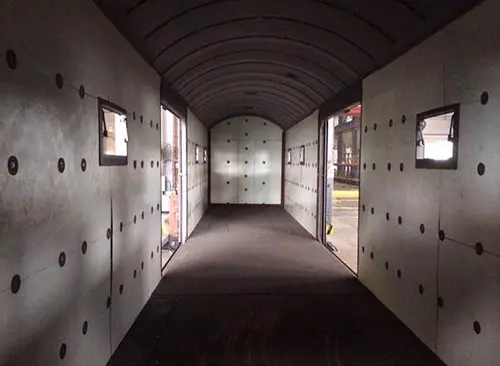
3.Lightweight Rail Transit. In the field of rail transit, a 3mm thick thin plate made of glass fiber PP unidirectional tape laminated by double belt press laminating machine is treated with flame retardant and applied to the inner lining of the shed car to replace traditional bamboo plywood, increasing the protection of the shed car body and significantly reducing the weight of the car body, ultimately achieving energy-saving effects.
4.Other applications in the field of transportation. Similar products abroad produced by double belt press laminating machine have also been applied to the anti scratch inner lining panel of box type truck wall panelsUnderstanding Double Belt Press Laminator Application in Automotive Lightweighting
Double belt press laminating machine can laminate fiber reinforced thermoplastic in continuous nonstop operation, therefore its application in automotive lightweighting is very popular nowadays.
1. Lightweight commercial vehicles. At present, automobile lightweighting mainly focuses on box type truck panels and passenger car structural components. The use of honeycomb panels with continuous fiber-reinforced PP laminated by double belt press laminating machine as the outer skin can replace the traditional fiberglass and metal cabin panels of box trucks. It can significantly reduce the overall quality of box trucks. According to statistics from relevant institutions, for every 100 kilograms reduction in car weight, fuel consumption per kilometer can be saved by 0.6 liters, overall vehicle quality can be reduced by 10%, fuel efficiency can be improved by 6% -8%, rolling resistance can be reduced by 10%, and combustion efficiency can be increased by 3%.
2.Lightweight passenger cars. Continuous fiber fabric reinforced thermoplastic laminated by double belt press laminating machine are currently more widely used by foreign companies in the lightweighting of passenger cars. The process of molding and injection molding thermoplastic composite sheets reinforced with fabric reduces the cost, reduces weight, and maintains good physical properties of the parts. By combining continuous fiber fabric reinforced thermoplastic composite materials double belt press laminating technology with injection molding technology, continuous fiber fabric made of PP resin is used to inject 30% fiber content PP modified plastic. Ultimately, the cycle time of the product was reduced to 39 seconds, the weight was 275g, and the cost was reduced by 44%. This molding method is also being familiarized by domestic enterprises, and relevant companies are conducting research and development on equipment and processes.